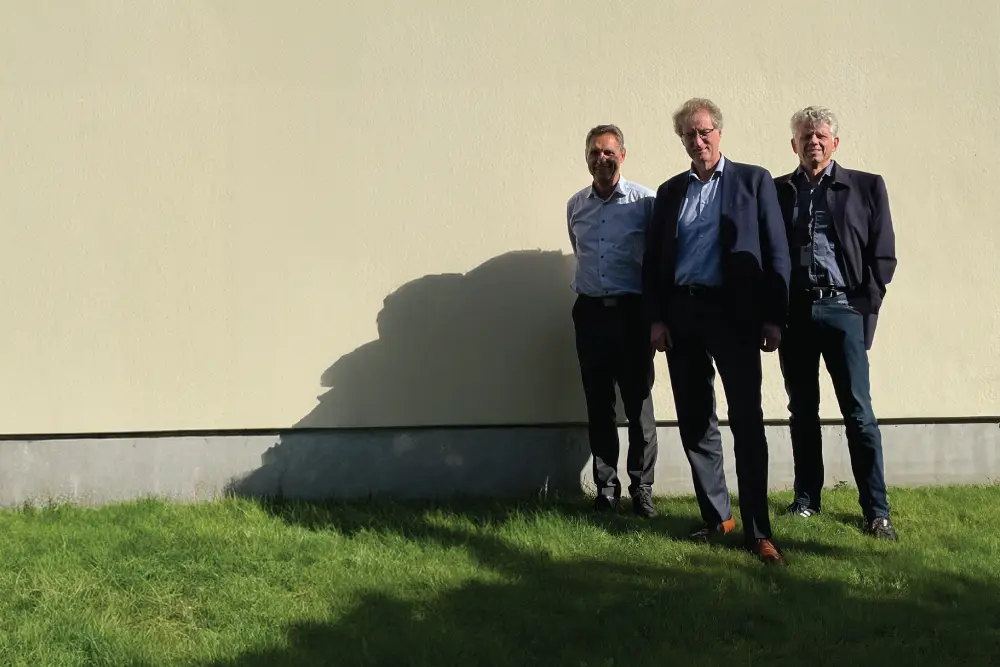
Equinor renews frame agreement with IFE, Stepchange and Epsis
We are pleased to announce that Equinor has renewed our framework agreement for an additional two years, with the option for extension (one + one year). This framework agreement is a collaboration between IFE, StepChange, and Epsis. This collaboration has strengthened our joint efforts for innovation, change, and efficiency in the energy sector through technology and operational improvements.
Eivind Madsen, CEO of StepChange, expresses great joy over the renewal of the agreement:
“It is exciting to have the opportunity to continue our productive collaboration with Equinor. This collaboration has already set high standards in the industry, and we are ready to take new steps together toward new technological and operational improvements. Equinor granting us this extension confirms that we have delivered high-quality projects together with an innovative customer. We are very proud of that!“
Our collaboration has focused on delivering practical solutions to address current challenges while also preparing for future opportunities. By leveraging IFE’s research expertise, as well as technology and innovation from StepChange and Epsis, we are shaping the future of integrated operations.
The extension of the agreement provides us with the opportunity to work together and hopefully set new standards for innovation and technological advancement.
Contact us
Let’s talk.
We would value learning about you and sharing some experiences!
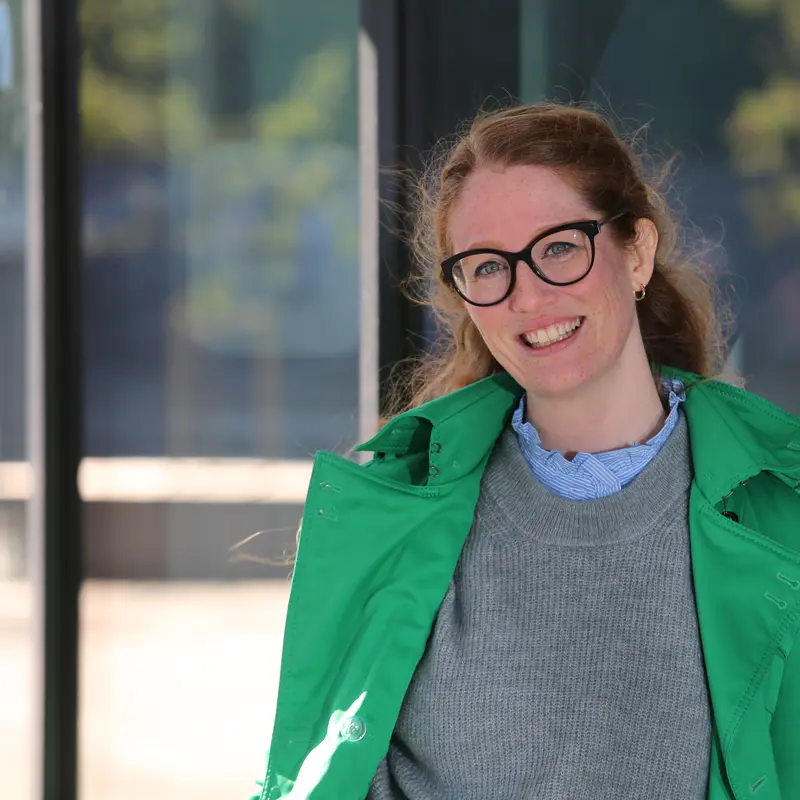