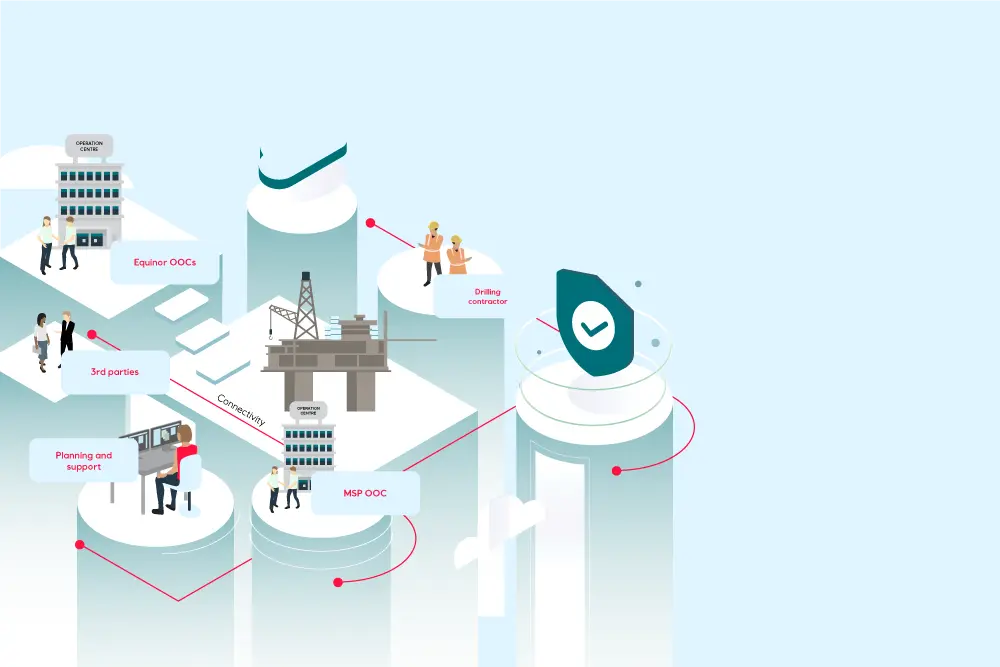
Epsis is awarded a broad roll out project for Virtual Operation Rooms (VOR) 2.0.
Epsis is glad to announce that Equinor has awarded us an exciting “Virtual Operations Room (VOR 2.0)” project. This project involves over 25 suppliers and 30 installations, rigs, and vessels. It is the first step in establishing virtual spaces for Drilling and Well’s operations. These are designed to create a space that gives you the same collaboration as being in the same physical room.
The project will use Microsoft Team’s B2B direct connect functionality to facilitate secure connections between Equinor and its suppliers.
The virtual spaces will allow the operational teams to work in a shared channel within their own company’s Teams. They will be able to communicate and share information seamlessly, without any barriers such as login issues, lack of access, or lack of management of who is online. An added benefit is the potential for a significant reduction in email communication.
We are looking forward to collaborating with the D&W team in Equinor. #digitalWork
Contact us
Let’s talk.
We would value learning about you and sharing some experiences!
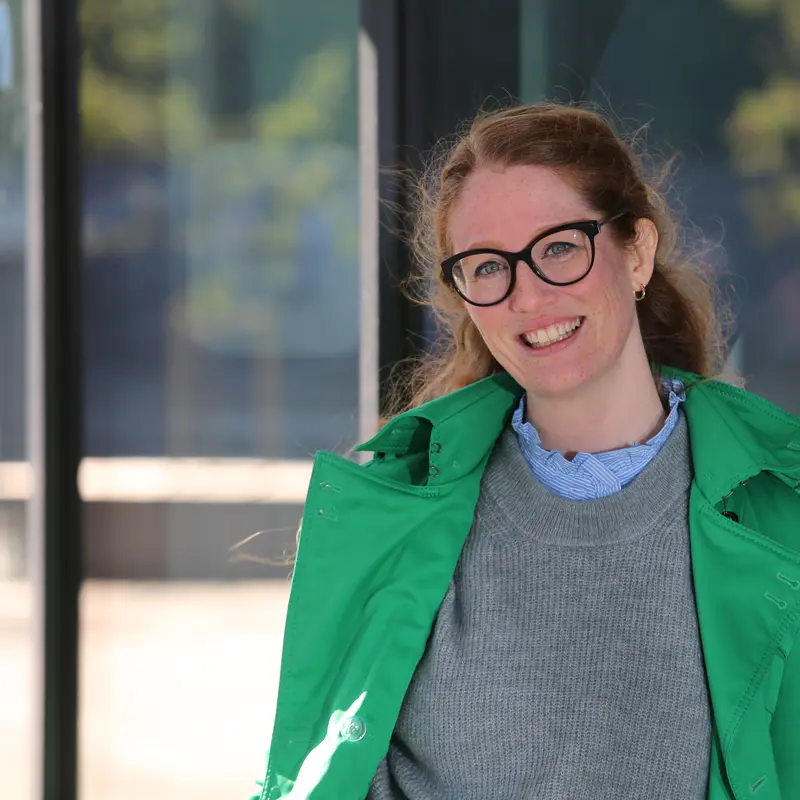